Feature Stair Series
Integrating Feature Stairs In Corporate Campuses: Key Considerations From Synergi’s Recent Projects
Sharing insights gained from its recent work on some notable campus projects, the following article highlights four considerations Synergi suggests keeping in mind when integrating feature stairs throughout large corporate campuses.
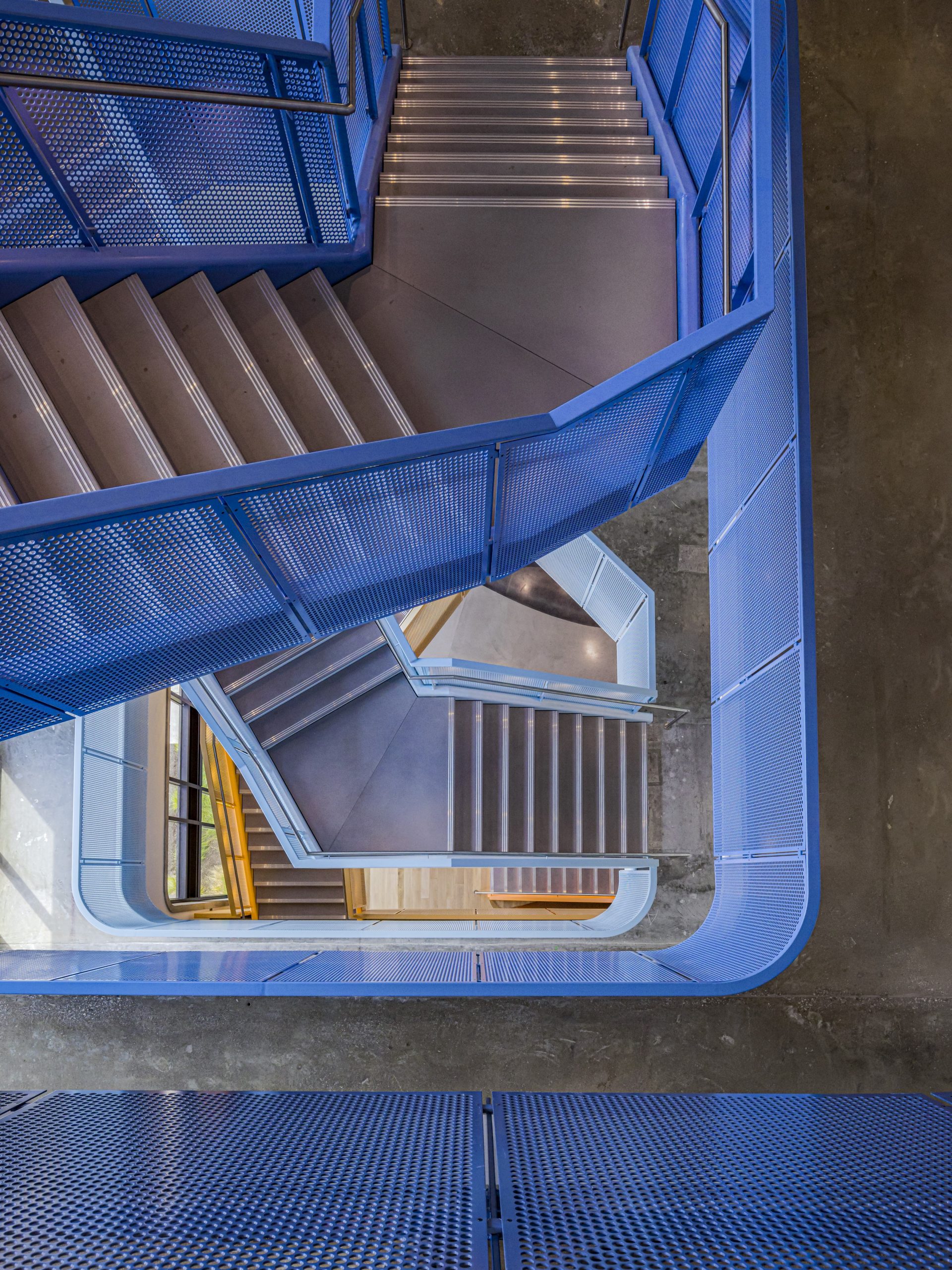
Feature stairs serve as central hubs in corporate campuses, encouraging movement, fostering collaboration, and enhancing the overall aesthetic appeal. These visually striking and functional elements create focal points that connect different parts of the campus, promoting a sense of community and interaction among employees. As feature stairs gain popularity in campus projects nationwide, understanding the benefits and challenges involved is crucial for successful implementation. Here are four key points to consider early in project planning.
1. Economies of Scale with Stair Stacks
Prefabricating multiple stairs with the same design significantly reduces costs and improves efficiency. By standardizing the design, materials can be purchased in bulk at a lower cost, and the repetitive fabrication process streamlines production. This approach not only minimizes labor costs by reducing the time and complexity of on-site construction but also lowers transportation expenses due to fewer shipments. Additionally, it shortens installation times, allowing projects to stay on schedule and within budget.
2. Sustainability and Environmental Impact
By engaging early in the process, Synergi is able to optimize the design and reduce carbon-intensive materials such as steel. One of the ways we do this is through prefabrication. Through our engineering process, we explore reduced-steel design options that still meet engineering constraints while honoring the design intent to determine whether prefabrication is possible for the project scope. Prefabricated stairs mean fewer truckloads are required, and there is less material waste during construction. Collaborating on the design early in the project also helps decrease change orders down the road, further reducing construction waste. This efficient approach supports a campus’s overall sustainability objectives, promoting a greener and more responsible development.
3. Prefabrication Saves Time
Prefabrication ensures that feature stairs are ready for installation much earlier in the project timeline. Efficient fabrication and assembly followed by minimally disruptive onsite installation saves months off a project’s schedule. Utilizing a controlled environment streamlines production processes for fast product turnaround – ideal for large projects with a high volume of stairs. Once assembled, prefab stairs are quickly craned into place onsite by Synergi’s nationwide erectors. Since all stick-built construction occurs on-site, the schedule is dependent on weather conditions and other factors. Modular elements, by comparison, arrive on-site up to 95% complete. Linear construction requires every step to be completed before the next can begin. Simultaneous in-factory and on-site work make modular construction up to 50% faster to occupancy. The time saved through prefabrication allows for earlier occupancy of the campus, providing immediate use of the facilities and reducing overall project timelines. This accelerated schedule benefits both the construction team and the end users, enabling quicker access to the fully functional campus spaces.
4. Turkey Approach vs Coordinating Multiple Trades
Instead of coordinating cost, scope, and schedule between 6-7 trades, Synergi executes stair projects with a complete turnkey approach. This method helps us capitalize on the benefits of early engagement with the owner, design, and construction teams to fill knowledge gaps in-house. With our turnkey approach, the single responsibility of the stair lies with one team. That team takes the project through all stages, including design assist, engineering, pricing, mockup production, final design and production, quality control, logistics, schedule, delivery, installation and sequencing, and finally, protection of installed materials.
SYNERGI’S RECENT CAMPUS PROJECTS:
Google Borregas Campus
One of Google’s first forays into mass timber building, 4 custom floating feature stairs connect the Googlers in the team space to each floor and the Café. Synergi’s scope of work included fully factory assembled feature stairs in blackened and ½” thick stained steel guardrails and treads that form a stair with no stringers. Through effective engineering and design options, the stair cost was reduced by 25% and the installation time for the fully prefabricated stairs was 10x faster than the original plan to stick build the stair in the field.
Walmart Home Office Campus
In 2019, Walmart began construction on its new Home Office in Bentonville, Arkansas, designed by Gensler to foster interconnectivity and walkability. The project, expected to be completed in 2025, features 12 mass timber office buildings within a campus resembling a walkable town square. Walmart partnered with Synergi to design and deliver 36 modular, prefabricated stairways, aiming to optimize design, reduce costs, and enhance sustainability. Early procurement allowed Synergi to standardize the stair structure design to gain economies of scale during fabrication and installation, reduce the amount of steel on each stair by almost 2,000 lbs, and minimize transportation-related carbon emissions, achieving a 35% reduction in embodied carbon emissions and significant cost savings.
Microsoft Atlantic Yards Campus
This key 400,000+ SF office space for Microsoft’s expansion in Atlanta, Georgia – part of the Atlantic Yards Development – features 7 completely unique feature staircases. Prefabricated into small, unitized assemblies, Synergi provided turnkey feature stairs, including precast treads, wood treads, steel structures, and guardrails. Streamlining the stair stringers and pre-fabrication into small units that could be traversed through the floor plates created a cost savings of 18%.
Ford Dearborn Campus
Set to open in 2025, the $1.2B dollar Research & Engineering (R&E) Ford Dearborn campus will house 6,400 Ford employees from a wide range of disciplines across its sprawling 700-acres. With multiple feature stairs and communicating stairs throughout, the 2 million sq. ft. Central Campus Building will create connections across floors, opening to daylight and minimizing travel distances while connecting employees together.
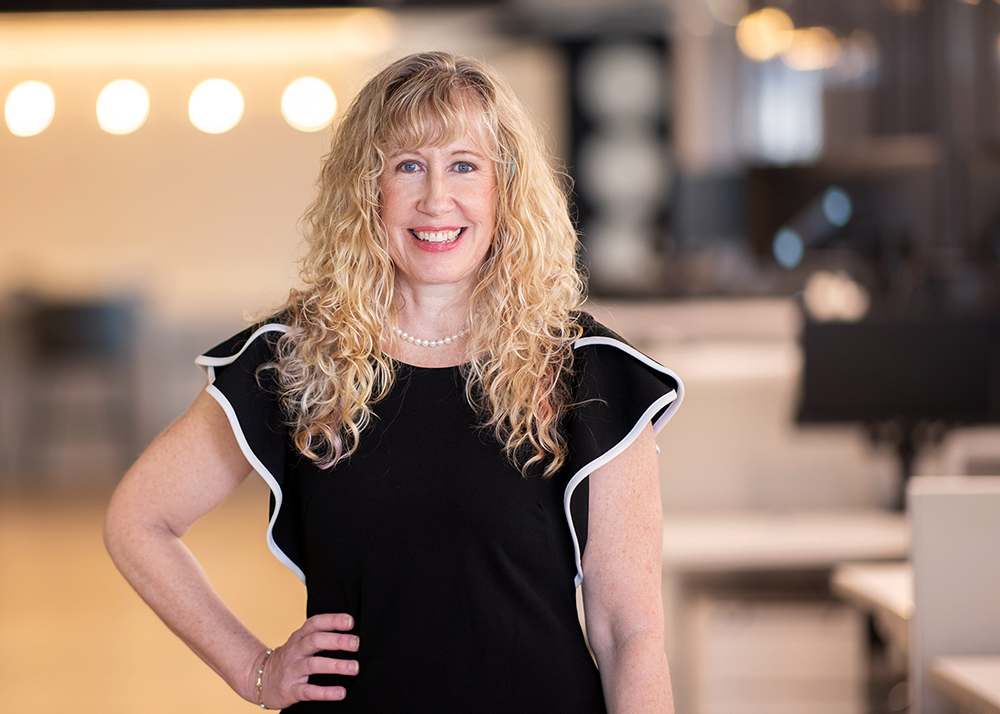
Synergi Welcomes Chief Operating Officer, Tracy Lea Neff
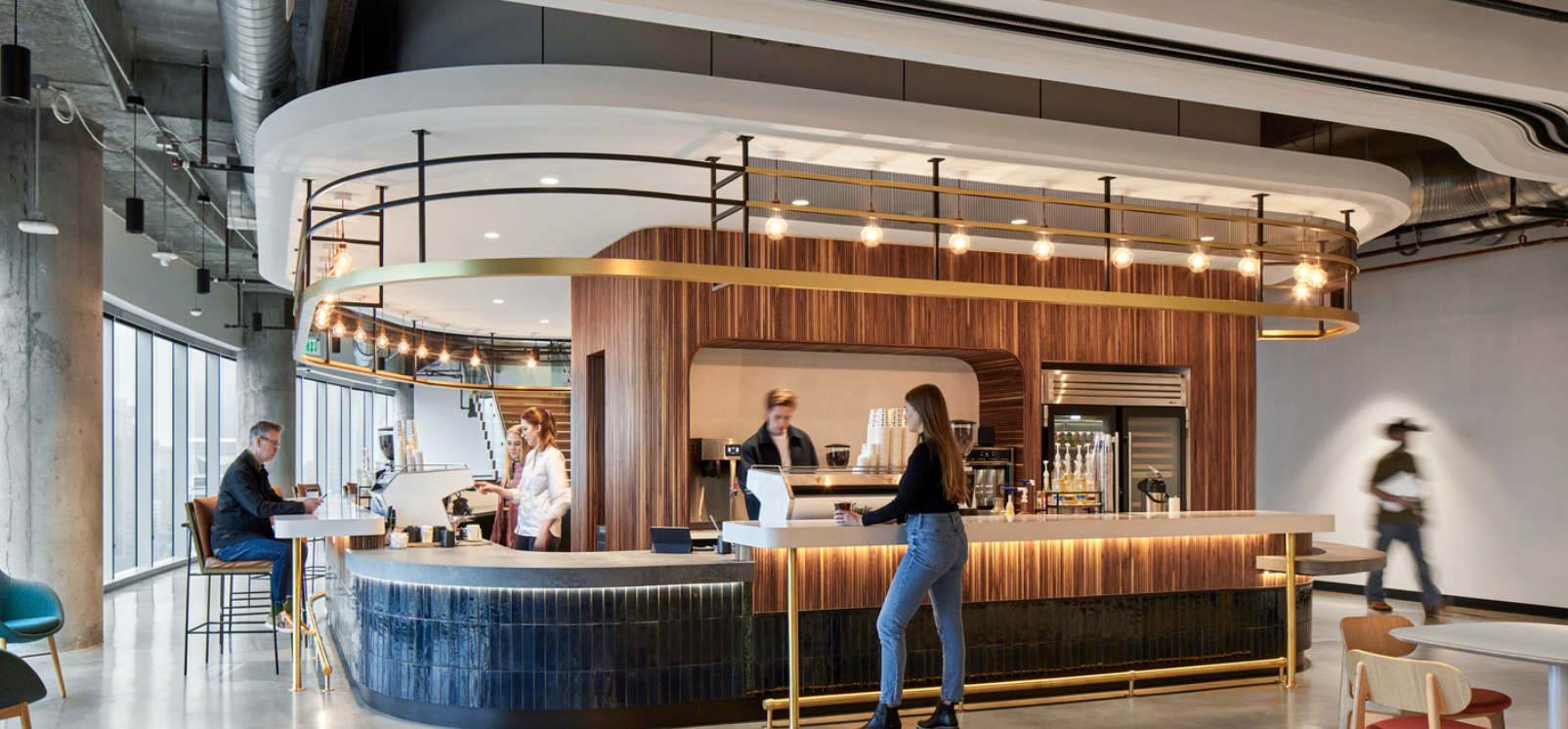