News
Synergi and Walmart: Scaling Efficiency with Prefabricated Stairs
Efficient design and smart engineering were at the forefront of Walmart’s new Home Office project, where Synergi delivered 36 prefabricated interconnecting stairs across 12 office buildings. Embracing Walmart’s "more for less" ethos, Synergi optimized the stair design, reducing steel usage by 86 tons and leveraging prefabrication to cut installation time from weeks to days. This innovative approach not only saved 15% in costs but also streamlined construction, helping to meet Walmart’s vision of a highly efficient, interconnected campus.
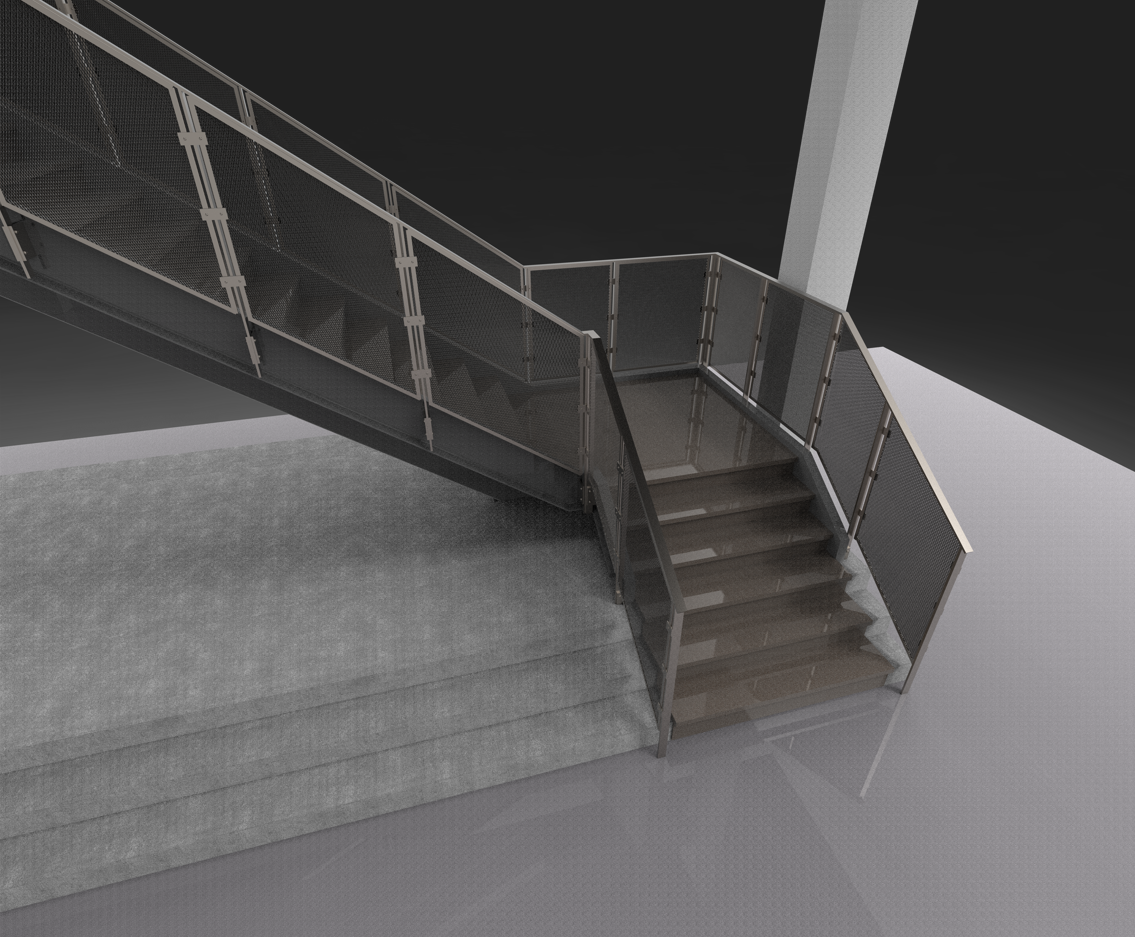
ABOUT THE PROJECT
In 2019, demolition, infrastructure, and utility construction began for Walmart’s new Home Office in Bentonville, Arkansas, anticipated to be completed in 2025. Citing its “proven track record of designing and building corporate campuses that reflect the culture, values and business needs of their clients,” in a press release, Walmart enlisted renowned global firm Gensler to serve as the executive architect. Walmart envisioned a campus centered on interconnectivity between coworkers, between the campus buildings, and between the natural and built environments.
Drawing upon its humble beginnings as a simple local store selling home goods in Northwest Arkansas, Gensler’s design for the new HQ is more akin to a walkable town square than a “traditional” office, consisting of 12 office buildings nestled among amenity buildings, parking decks, and outdoor spaces atop approximately 350 acres of rural Arkansas land when the project finishes in 2025. The inspired design emphasizes walkability, proximity, and the opportunity for people to have creative collisions that fuel innovation and a sense of camaraderie within the overall campus.
OBJECTIVES
Walmart commissioned each partner to adhere to its more for less culture through every step of the project – not by cutting corners but through smart design. With this pursuit in mind, Walmart worked with the team at Synergi to find a smarter, smoother, and more profitable way to deliver all 36 interconnecting stairways interspersed throughout the 12 office buildings from Gensler’s inspired design.
Our goal is to ensure the project is efficiently designed and manufactured in a controlled environment for consistent performance.
Walmart Spokesperson
SMARTER DESIGN
Walmart engaged Synergi to find a solution – in line with its more for less ethos – to deliver the many stairways so crucial to creating the open, collaborative environments it envisioned. Soliciting our methodological approach for discovering design optimizations and installation efficiencies, the company challenged us to execute their concept of a single “drag and drop” design that could be used across all 36 stairs. By using a single, replicable design, Walmart hoped to optimize and expedite the design and construction processes.
OUR APPROACH
Determined to honor Walmart’s commitment to a project that is efficiently designed and manufactured in a controlled environment, Synergi’s team focused on finding ways to maximize the impact of our scope of work early in the design process. Our stair experts determined three key areas to promote Walmart’s goal:
- Design Optimization
- Prioritizing Prefabrication
- Streamlining Transportation
DESIGN OPTIMIZATION
Through our engineering process, we explored reduced-steel design options that would meet engineering constraints while honoring the design intent. By changing member (stringer) sizes, we landed upon a design that met these criteria while still allowing for a modularized model. An extremely dense and heavy metal, our team realized we could further optimize the design by removing additional steel, uncovering an opportunity to prefabricate the stairs and lift it into the building structure as one unit. To make this design work, the stairs had to be as light as possible so each run could be craned into place in one complete section.
Across the 36 interconnecting stairs, all of the railings, tread supports, guardrails, and picket guardrails were designed and engineered to reduce steel usage. By reducing the size of the tread support, 540 pounds of steel was eliminated from each stair, reducing total steel by 10 tons. Additional savings of 76 tons of steel was created by modifying the design of the steel guardrails. The combined reduction of 86 tons of steel not only significantly lightened the load for a prefabricated installation, but also drastically reduced embodied carbon emissions resulting from steel manufacturing.
BENEFITS OF PREFABRICATION
Not only did prefabrication keep us in line with Walmart’s goal for manufacturing in a controlled environment, but it also offers several additional benefits, as well. Because prefabrication takes place in a controlled environment, the final stair product is typically of better quality than its traditional onsite “stick-built” counterparts. And, because the entire stair section is already assembled upon arrival to the job site, installation time is reduced. The difference in time spent onsite diminishes from an estimated two to three weeks per stair section for traditional installation approaches to as little as two to three days.
These time-savings have a snowball effect – the sooner the stairs are installed, the sooner other trades can resume their work. The collective effect of the diminished timeline for the individual elements can make a significant impact on the project’s schedule overall – especially applied across 36 stairs – which generally has a positive impact on the budget, as well. Design reuse and replicated production processes also eliminate the costs integral to developing many varying designs and each design’s ensuing production processes.
REDUCING TRANSPORTATION POLLUTION
REDUCING TRANSPORTATION POLLUTION
Our decision to prefabricate Walmart’s stairs provided the opportunity to further reduce cost by minimizing our time onsite. Transportation of monolithic steel components is traditionally cost and pollution heavy. Traditional “stick-built” stairs require many shipments to be made to the jobsite to transport the building materials, crew members, and left-over materials and construction waste away from the job site upon completion.
Prefabricated stairs, by comparison, can be transported to the job site in fewer and more compact shipments. By minimizing the number of truckloads, transportation’s cost significantly decreases. While traditional stick-built stairs would have required 108 truckloads, Synergi’s prefabricated stairs required only 36 truckloads.
OUTCOME
Synergi’s early intervention in this project allowed the team to optimize the design (reducing the amount of steel used), expedite the installation (by prefabricating the stairs), and minimize the project’s transportation needs for fewer, more compact shipments. In total, these efforts resulted in cost savings of 15%!
The new Walmart campus will embody the DNA attributes for a connected and successful workplace with the latest advances in technology and sustainability, while reflecting the Walmart culture and seamlessly integrating into the fabric of the community.
Douglas C. Gensler, AIA, NCARB, Gensler Principal and Managing Director
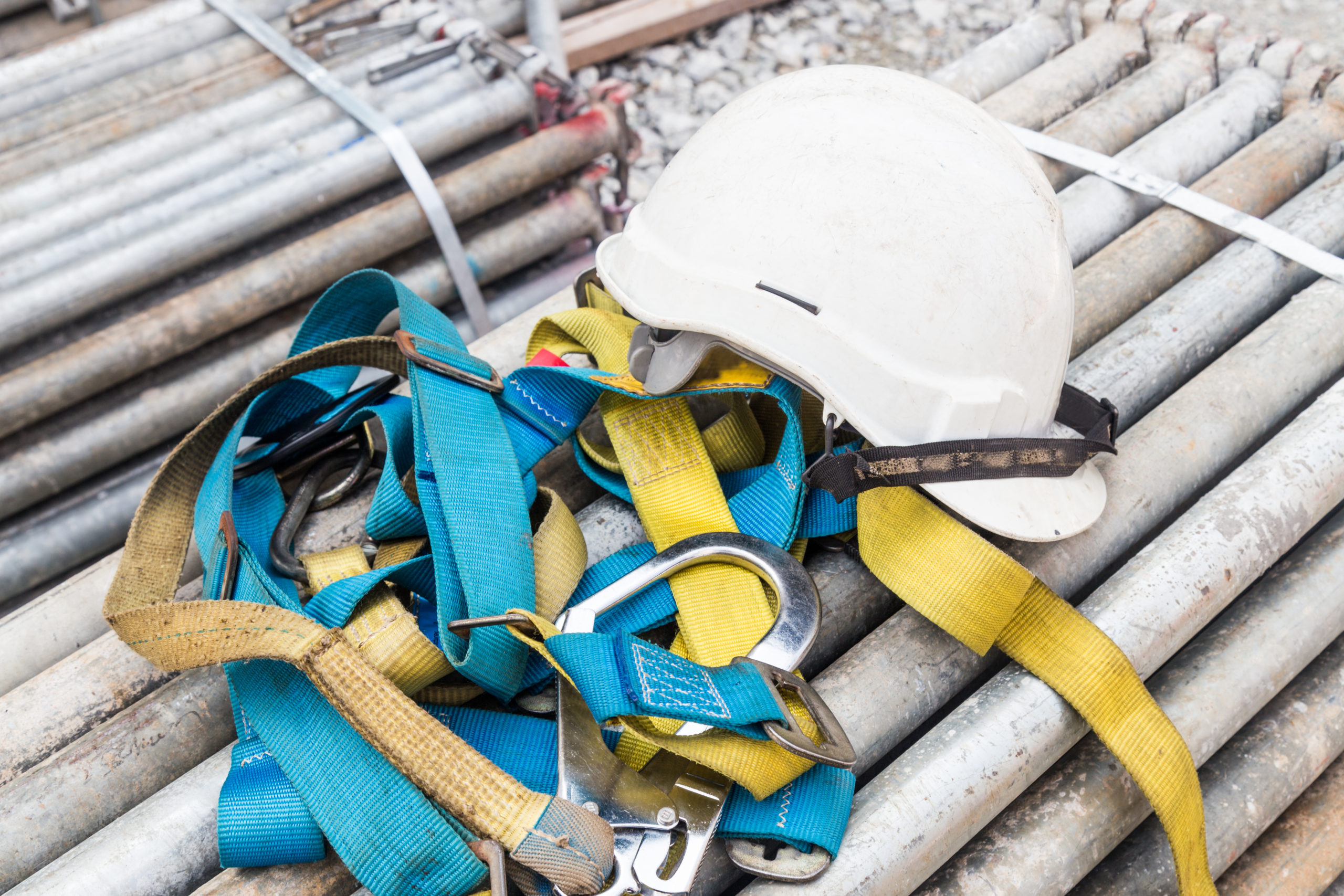
Synergi Safety Officer Scott Harman Speaks to His Experience in the Industry
