News
Synergi’s Feature Stair for Printemps’ U.S. Debut
When Printemps set out to open its first U.S. flagship at One Wall Street, the vision was a space that blended Parisian elegance with modern luxury—more than a department store. At its center: a sculptural helical stair, both a tribute to the building’s history and a bold design statement. Synergi brought this vision to life with a sweeping stair featuring illuminated marble treads, brass handrails, and intricate millwork—equal parts engineering feat and architectural showpiece.
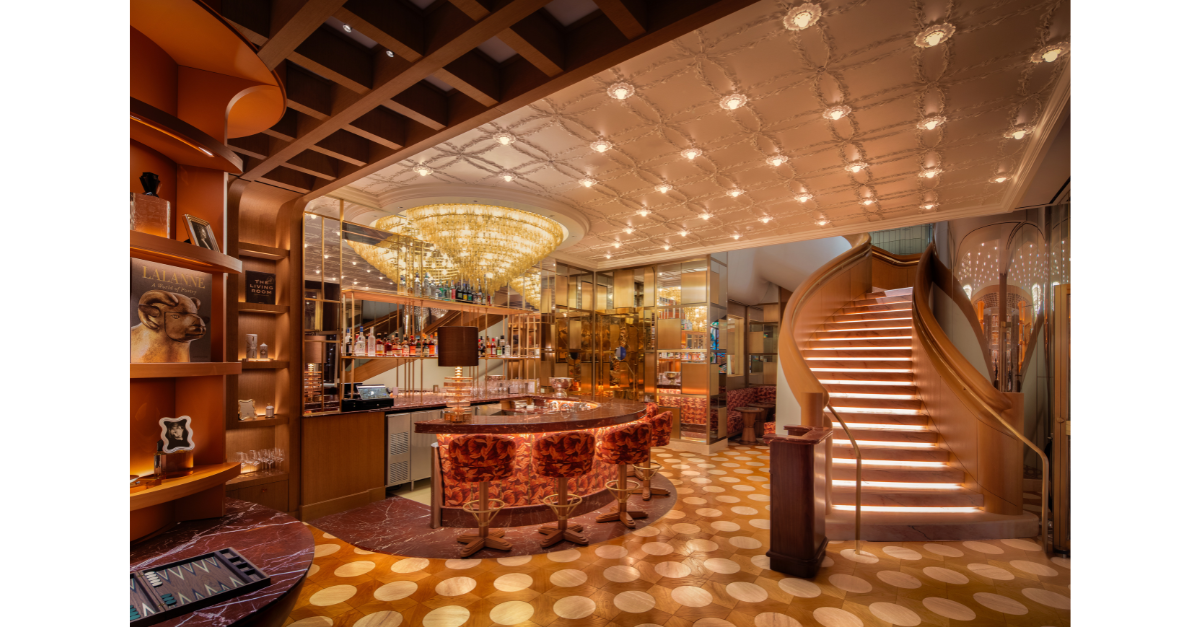
ABOUT THE PROJECT
When Printemps, the iconic French department store, set out to open its first U.S. flagship inside the landmark One Wall Street building, they envisioned a space that fused Parisian elegance with contemporary American luxury. At the heart of this transformation would be a sculptural, curved stair—a signature architectural element that needed to both honor the history of the space and Printemps vision to be ‘more than a department store’. Synergi was tasked with turning this vision into reality. The result is a sweeping helical stair featuring illuminated marble treads, brass handrails, and complex millwork—an engineering and fabrication feat as much as a design showpiece.
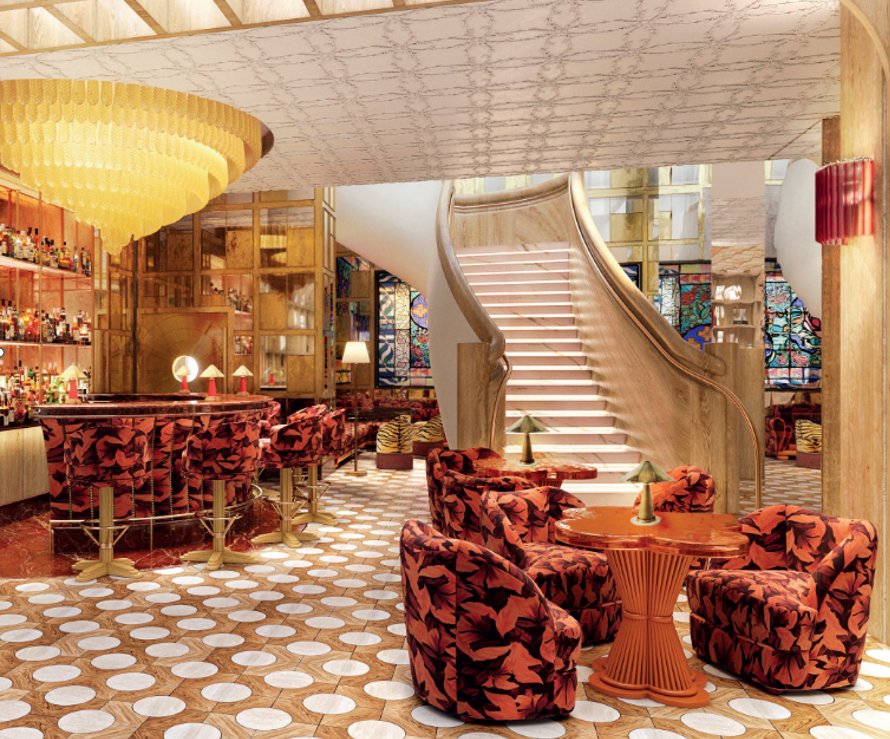
Initial Rendering
Designed by French architect Laura Gonzalez, the stair features a helical form with compounding radii, visible in both its steel substructure and the millwork components that wrap around it. Located within a restored Art Deco skyscraper—and with active tenant spaces above and around—this stair had to be constructed with minimal disruption.
From the beginning, Synergi’s preconstruction team worked closely with the design team to translate the European design intent into a U.S.-code compliant, buildable solution. The stairs’ structure, finish, and geometry were all tightly coordinated through digital modeling, helping us anticipate constraints and plan field workflows long before installation began.
COMMUNICATION WITH DIGITAL MODELING
The complex nature of this geometry required visual communication with the multiple trades it took to fabricate and coordinate. Synergi’s Detailing team modeled the stair using software capable of exporting in various file formats to visually communicate in 3D with clients, fabricators, and erectors. This presented the ability to diversify the communication style using the same reference model in 1:1 ratio down to the exact number of bolts represented in the model. This proved exceptionally useful in our most complex forms, the gooseneck transition, which proved difficult communicating in 2D. Presenting in 3D also opened the conversation to suggestions by our steel frame fabricators who were able to visually communicate their fab recommendations, ensuring a stronger and more robust product.
FIELD COORDINATION WITH MINIMAL DISRUPTION
The framework of the stair is made of structural HSS tube steel crafted with precision to construct the helical form. Divided into sections, the Detailing and Construction team needed to coordinate how to carefully anchor the 7,000-pound steel frame into place. Built in 1931, the historical features of the building were not only decorative but also structural. The building’s framework is built using Carnegie Steel embedded in a thin layer of concrete. Synergi coordinated with the Whole Foods business located a floor below to chip away at the concrete slab and weld the stair directly onto the beams. This required a high level of coordination as the grocery business is a 24-hour operation that we would be disrupting for our stair erection.
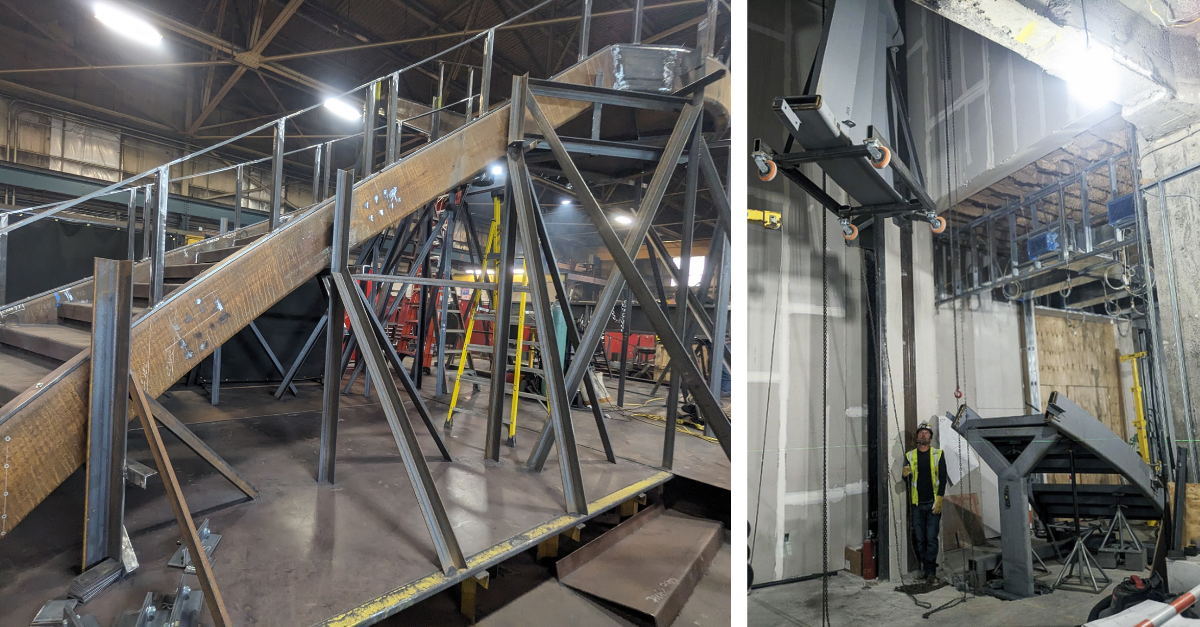
Fully Assembled Steel Structure In Fabrication shop (left), Modular Stair Sections Arriving For Final Assembly Onsite (right)
DIGITAL FABRICATION MEETS HANDS-ON CRAFT
One of the most striking elements of the stair is its continuous white oak top cap. Crafted from solid 200-pound sections, each piece was CNC-machined on a 7-axis mill to achieve the stair’s complex curvature—including gooseneck transitions at landings and turns. The geometric uniqueness of every segment introduced additional complexity: each handrail bracket needed to be drilled at a custom angle and depth.
To solve this, Synergi developed 3D-printed plastic drilling jigs that slotted precisely into the oak profile and provided the exact orientation for each bracket. This not only ensured consistency and accuracy, but also saved time in the field and reduced margin for error.

White Oak Top Cap Sections
We also produced full-size 3D-printed top cap templates that allowed us to begin layout and bracket installation before the final oak material arrived—an essential move given lead time challenges and the project’s fixed opening date.
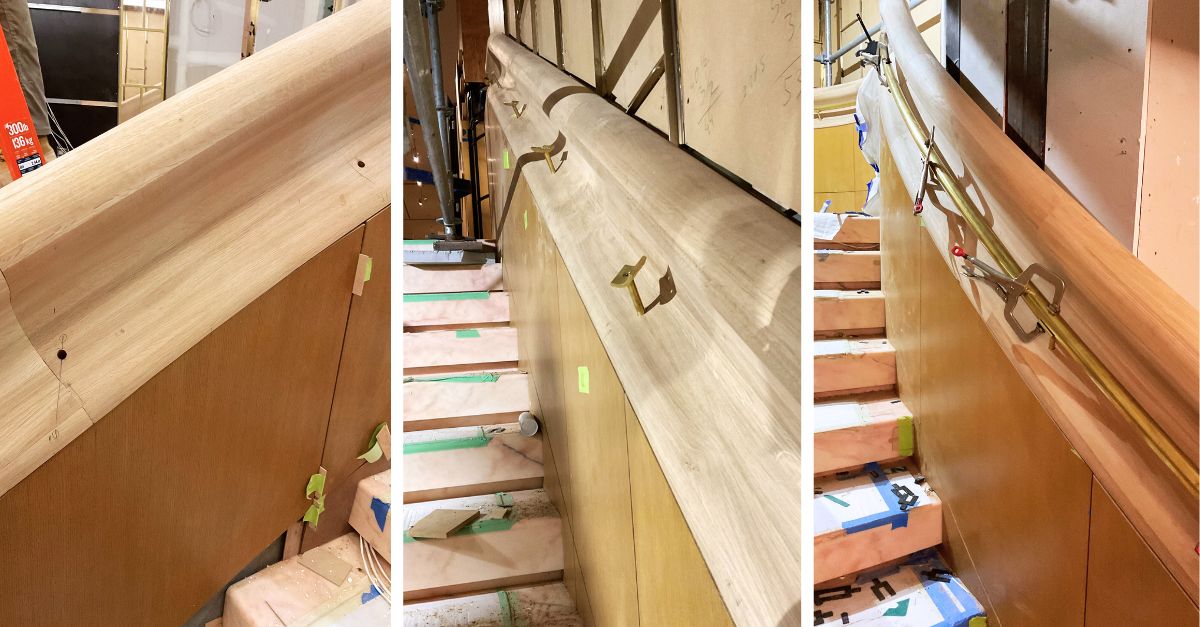
Brass Handrail Installation
PRECISION FIELD FINISHING
Precision carried through to the finishing phase. All millwork—including top cap and curved guardrails—was finished in the field to allow for real-time adjustments and seamless transitions between wood surfaces. Our team hand-adjusted stains on-site to ensure perfect color matching under real lighting conditions, using high-grade pigments and tight control over application.
Brass handrails, another material chosen for its warmth and elegance, posed their own set of fabrication challenges due to the material’s unique structural limitations, welding properties, and finishing demands. We worked closely with the design team to submit multiple rounds of samples showing the effects of various welding rods and finishing oil, and how they effect the natural brass patina over time. Finishing of specialty metals is often an exercise to balance up front costs, desired patination and maintenance costs. Synergi was able to utilize our in-house design expertise to find a solution that worked for all parties, and will withstand the test of time. We worked closely with specialty partners to fabricate and install these elements to exact tolerances, while maintaining the delicate finish.
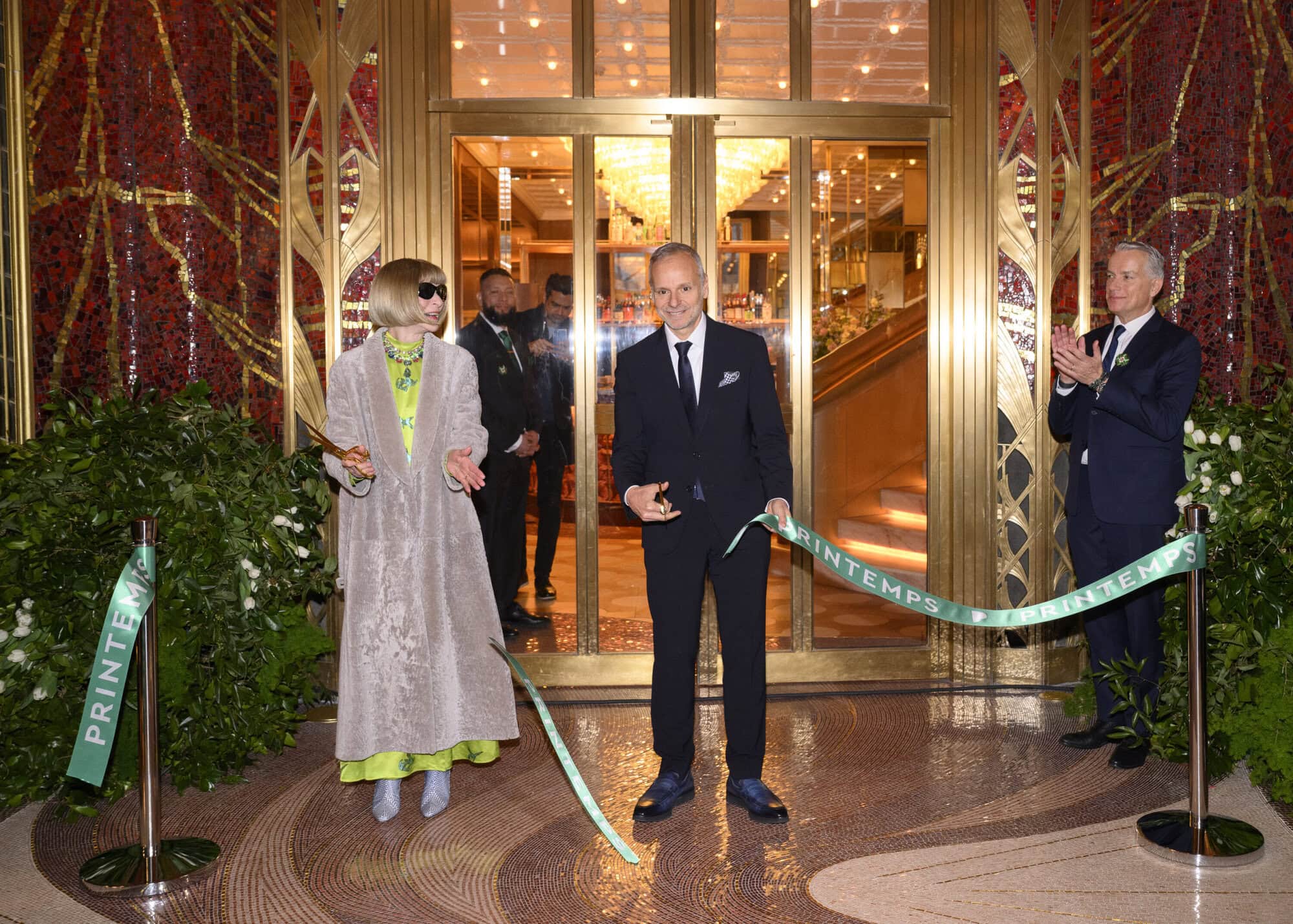
Anna Wintour, Jean Marc Bellaiche at Printemps Grand Opening
DELIVERED WITH PURPOSE
With a high-profile opening on the horizon—featuring Vogue’s editor-in-chief and other major press—there was no room for delay. Synergi’s integration of digital tools, fabrication expertise, and on-site problem solving allowed the team to meet an aggressive schedule while maintaining the level of finish expected of a global luxury brand.
More than just a way to move between floors, the stair stands as a sculptural centerpiece and a testament to thoughtful, detail-driven construction. For Printemps, it marks an ambitious and refined entry into the U.S. market. For Synergi, it’s a showcase of what’s possible when design vision meets expert execution.
RECENT PRESS:
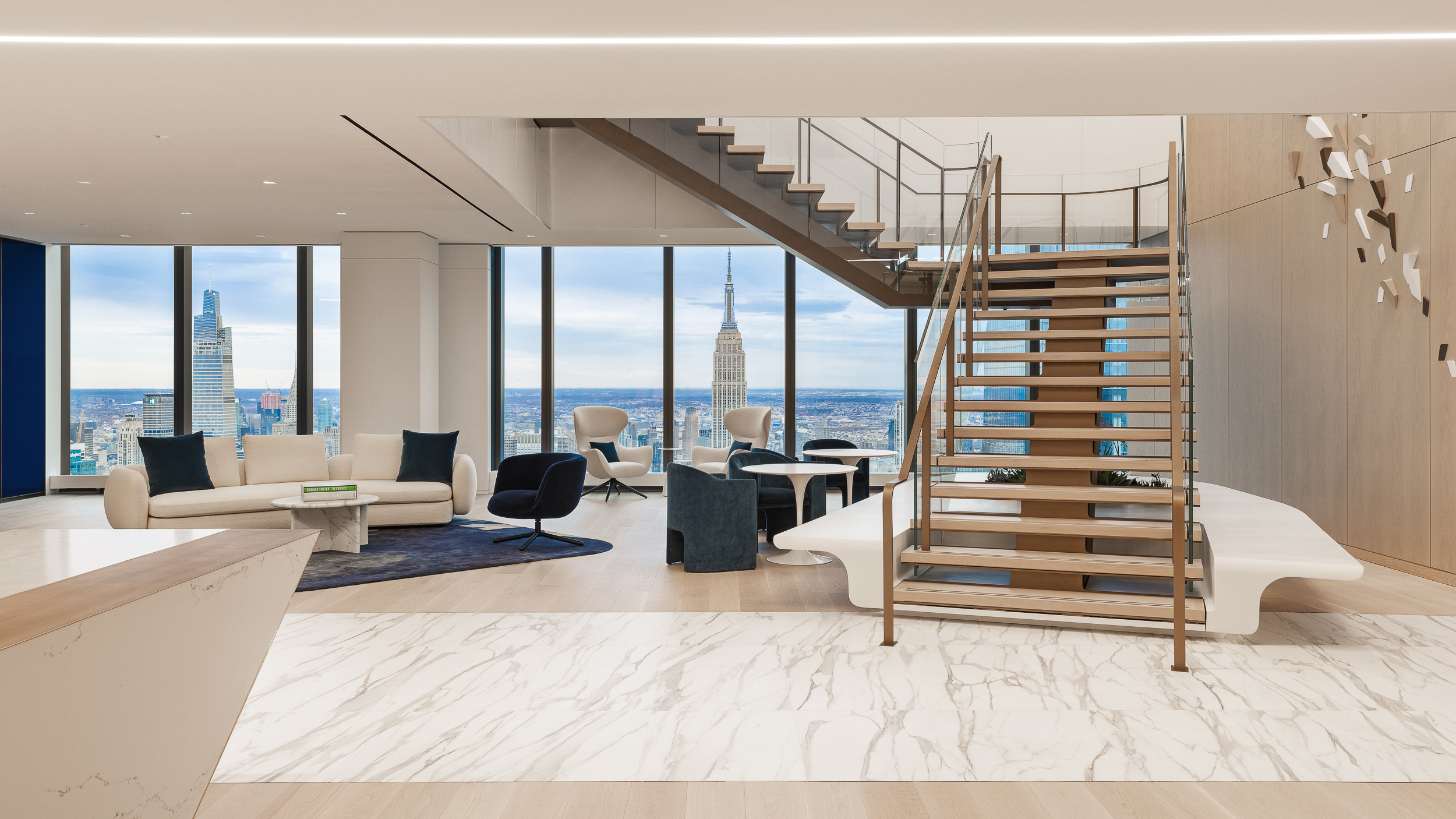
Synergi’s View‑Centric Feature Stair at 50 Hudson Yards
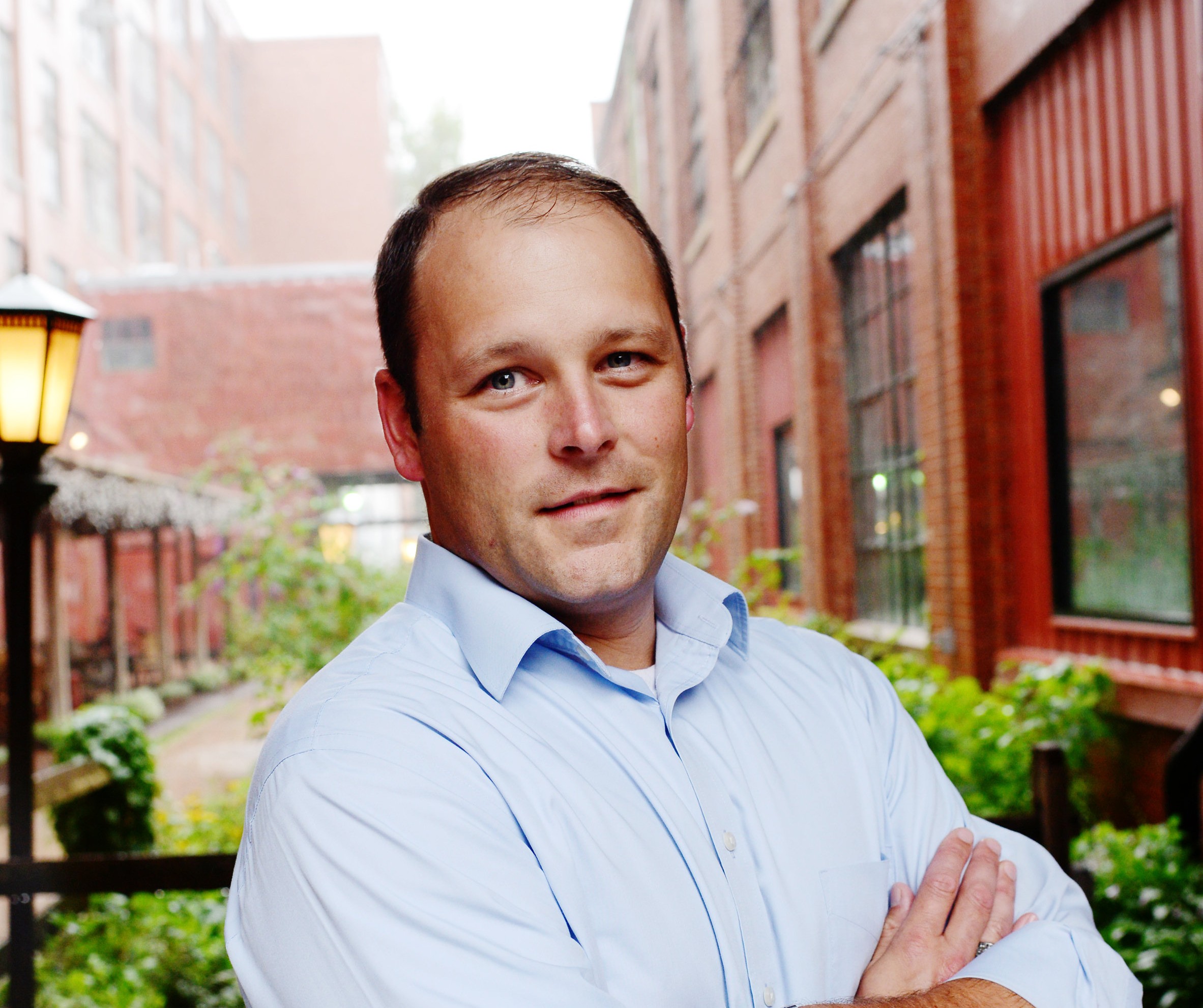