News
Early Engagement: The Solution to Supply Chain Setbacks
Like many others in the construction industry, 2021 and 2022 presented our team with a slew of production issues stemming from supply chain setbacks and material and labor shortages in the shop and field. Upon collaborating with our sustainable steel mill partners and internal production/operations teams, Synergi has established an integrated stair delivery at risk process to guarantee material and production slot availability for significant/key projects.
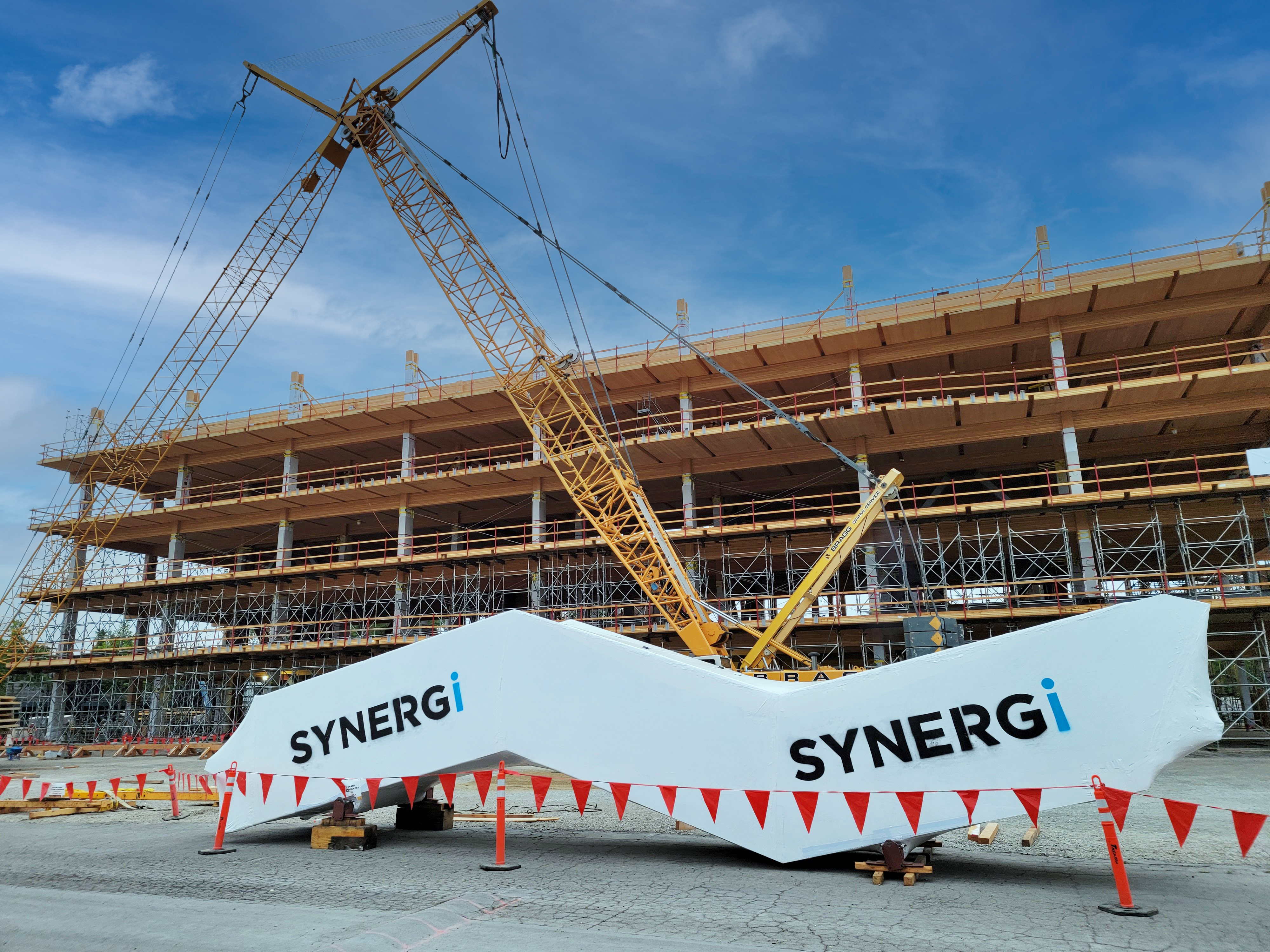
By collaborating with our sustainable steel mill partners and internal production/operations teams, we were able to analyze lessons learned in 2021 and establish a strategy that combats supply chain risk in 2022 and beyond.
Our findings revealed that in order to maximize economies of scale on core and shell/ground-up projects, we should ideally engage our project team at a minimum of 18-20 months before a projects’ building structure erection commences. For tenant fit-out projects, where the project timeline is more compact, the best approach is to engage a subcontractor in the early stages of design to collaborate with and inform the designer of supply chain issues relevant to their design and mitigate any irreversible design decisions that could create supply chain risk.
To guarantee material and production slot availability for significant/key projects, we need to engage our project team at a minimum of 18-20 months prior to the start of building erection.
– Jim Admiraal, CO-CEO at Synergi
Despite this approach being a notable shift from past project delivery methods, Synergi has documented its success with standardized early engagement on large campus projects for clients including Walmart, Ford, and Amazon throughout 2021. In this article, we dive deeper into why we believe early engagement is the new normal in a post-pandemic world.
WHY EARLY ENGAGEMENT MATTERS ON PROJECTS WITH STAIRS
The majority of Synergi’s projects involve custom feature and interconnecting stairs. These stairs are complex. Why is that?
Stairs are not an off-the-shelf item. They commonly evoke confusion and uncertainty for the parties involved – specifically surrounding costs and delegated engineering risks. West Coast projects, for example, require unique and potentially concerning considerations – such as seismic movement, harmonics, and vibration – and identifying and controlling these risks often puts pressure on the schedule. Therefore, the earlier design challenges can be resolved, the greater the control of project costs.
Engaging 18-20 months early allows Synergi the required time to design and engineer the most efficient material sizes, connections and modularize the design around logistical constraints, resulting in a design that is meticulously refined to fit the desired budget. The present supply chain crisis has surfaced multiple uncertainties for significant or key projects. When it comes to modular communicating stair systems, the main concerns often revolve around material sourcing and the availability of labor within the supply chain and field for installation.
Synergi’s proven benefits of engaging in a project 18-20 months before the actual construction provide valuable time for:
-
- Launching Synergi’s Design-Assist Process
- Procurement of Materials (i.e., long lead items such as custom steel shapes, aluminum extrusions, and materials such as glass that have experienced recent supply chain uncertainty)
- Connection Design
- Engineering and vibration analysis
- Embed Design and Placement
- Mill Orders for Materials
- Mockups
- Material Finish confirmation
- Finished Samples
- Constructability Reviews and Testing
- Fabrication
- Creating engineered Rigging Plans
- Early release of high-risk items building in a buffer where they are stored before needed on site
- Sequence Scheduling to Optimize the Use of Site Cranes and Other Equipment
- Securing installation welders (union/open shop) for onsite erection/installation of stairs
To make early engagement achievable, there needs to be an understanding of what this process looks like for Synergi’s projects. From there, we can break down exactly why early engagement has proven to reduce supply chain complications and delays.
WHAT DOES EARLY ENGAGEMENT MEAN TO SYNERGI?
Early engagement means that the resources and expertise offered by each link in the supply chain are considered at the very beginning of the design process to inform the initial design.
As industry leaders in the design-assist process, Synergi is the driving force behind collaborative efforts that capitalize on early engagement.
Under Synergi’s Design-Assist project delivery method, the design team (owners and architects) engages with the pre-construction team (estimators, detailers, and project managers) at the beginning of a project to improve constructability and reduce the overall time and cost. These key stakeholders develop a strategy for producing the stairs successfully, addressing concerns for the plans early in the design process rather than after construction documents are completed, when it is often too late to address issues efficiently and cost-effectively.
For design-assist to produce the desired results, early engagement is key.
Not only does early project involvement result in more informed decision-making as the project continues, but it also creates flexibility to relocate resources to the items that have the highest priority in the design intent.
For example, long lead-time items are identified and pre-ordered if there is a risk to the schedule. In a traditional project involving stairs, an architect designs a stair and has the engineer of record develop the structural element drawings and details. From there, the general contractor typically puts the project out to bid and gets prices from a variety of sub-contractors. Cost overruns are identified at this point triggering value engineering and delegated engineering and logistical risks are not realized until the project is in the shop drawing phase and options to mitigate these risks and protect the design intent are limited. Design-assist alters this narrative.
By having collaborative design meetings commence 18-20 months prior to the start of construction, Synergi can fully grasp an architect’s vision for the project, and subsequently, finalize the stair design to the budget addressing constructability, engineering, and schedule risk, preventing the inevitable cost issues and delays that traditional methods face.
In essence, Synergi’s design-assist process allows us to maximize resources across the project for the betterment of the schedule and budget. Simply put, achieving this result comes down to planning and designing for months rather than redesigning during the shop drawings process that impacts the schedule, budget, and design intent.
In 2020, 90% of Synergi’s projects used the design-assist process.
HOW EARLY ENGAGEMENT HELPS REDUCE SUPPLY CHAIN DISTRESS
After analyzing project trends and results over two years of heavy industry-wide supply chain disruption, Synergi has witnessed the benefits of early engagement first-hand.
Developing Stronger Supplier-Manufacturer Collaboration
Because of the importance of collaboration, early supplier team involvement strengthens ties amongst supply chain participants. The more everyone is invested in the final product, the more innovation is enabled.
Quickened Response Time and Enhanced Problem-Solving Skills
When designers and engineers communicate earlier and more effectively with fabricators, different skill sets are combined, resulting in more innovative and effective problem-solving solutions. The design-assist team can identify unworkable design concepts early and provide alternative options. Close communication among pre-construction and production accelerates the overall project team’s ability to respond to problems.
Mitigation of Sub-Supply Chain Issues
Each link in the supply chain has varying schedules based on the many projects being considered for production at any one time. Early engagement allows Synergi to contractually confirm with a vendor (such as a glass fabricator or precast tread fabricator) once the design has been finalized to lock the needed production slot – in turn allowing our vendors to procure materials and mitigate the risk of delay.
Shortened Product Development Cycle
Production plans are frequently communicated back and forth between suppliers, engineers, and production throughout the product design process with each link in the supply chain. This is due to a lack of early communication between the various production departments. Continual back-and-forth interchange lengthens lead times, raises expenses, and lowers productivity. By boosting early fabrication and pre-construction engagement, the product development cycle is immediately shortened.
THE ROLE OF DESIGN-ASSIST IN SYNERGI’S SUPPLY CHAIN SOLUTION
For more than 35 years, Synergi has used its empirically developed design-assist methodology to collaboratively optimize design features with engineering or budgetary constraints. By purposefully addressing concerns early in the design process, we enable the project’s key stakeholders to proactively develop a strategic final design. Through our Design-Assist method, a project’s team can utilize Synergi’s specialty expertise to fill knowledge gaps in budgeting, materiality, and constructability to successfully achieve the delicate balance between creativity and constructability within the limitations of schedule and budget.
Design-Assist is, at its core, a collaboration between a project’s key stakeholders about vision, design intent, and constructability. During the Strategy phase, Synergi visits with a project’s design team and construction team to understand project constraints and design priorities, identifying potential risks to arrive at the highest quality and most efficient design possible. The Synergi team also provides extensive benchmarking discussions to ascertain the priority of each item’s level of finish against achievability within the budget. So, when it comes to safeguarding the supply chain, Synergi’s design-assist approach is a unique contributor in terms of early engagement.
RESULTS OF EARLY ENGAGEMENT
In a recent $5B redevelopment project, Synergi’s initial scope involved 16 stairs across 4 buildings, complete with integrated design-assist to identify seismic movement, vibration analysis, and code compliance as they tie into constructability.
Synergi’s involvement in this project included a full design-assist process starting at 100% SD. Our team provided turnkey floating monumental steel stringers, field painting, wood treads, and guardrails. This included cost benchmarking, cost optimization, pre-construction design, engineering, shop drawings, rigging, transportation, fabrication, and installation.
Ultimately, Synergi streamlined the design of 26 (rather than the initial 16) stairs to be similar and modular in design to gain economies of scale while still providing a unique experience and stair for each building.
Combining early engagement with our design-assist process resulted in a 30% savings compared to the initial cost of the project.
Synergi feels that to remain competitive, we must take into consideration the overall effectiveness of our supply chain. Focusing on early engagement not only results in more informed decision-making as the project continues, but also creates flexibility to allocate resources to the items that have the highest priority in the design intent. By seeking design assistance early in the process, Synergi not only leads the design regarding constructability but also controls costs in a way only achieved by strategic collaboration between owners, architects, and subcontractors. Although this process differs from past project delivery methods, we have implemented early engagement on large campus projects including Walmart, Ford Amazon in 2021 and believe this is the new normal in a post-pandemic world.
Citations:
Analyst, X. W. R. (2022, January 4). Post-covid lead times. Cumming. Retrieved February 8, 2022, from https://cumming-group.com/post-covid-lead-times/
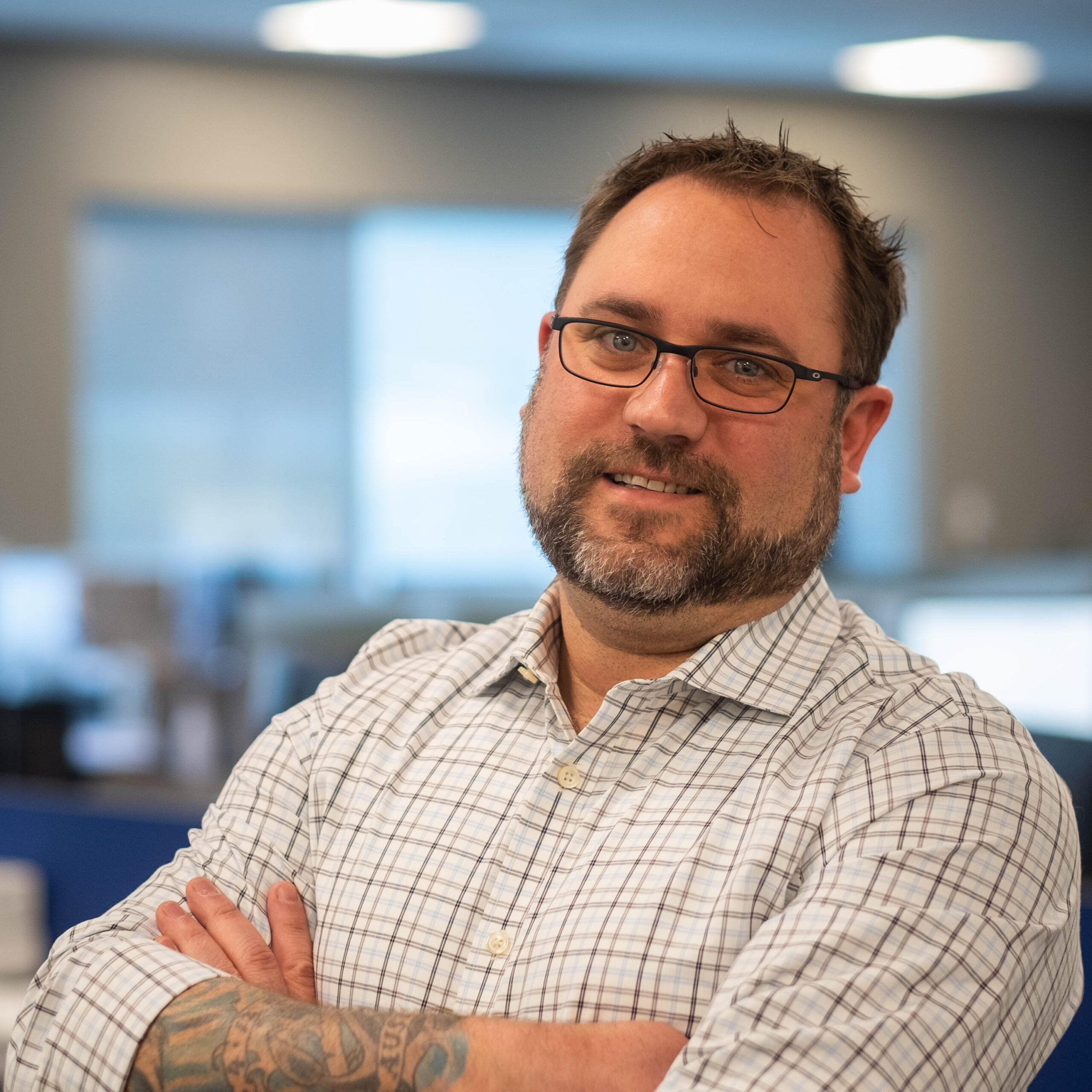
Welcoming New Senior Pre-Construction Manager Adam Suchta
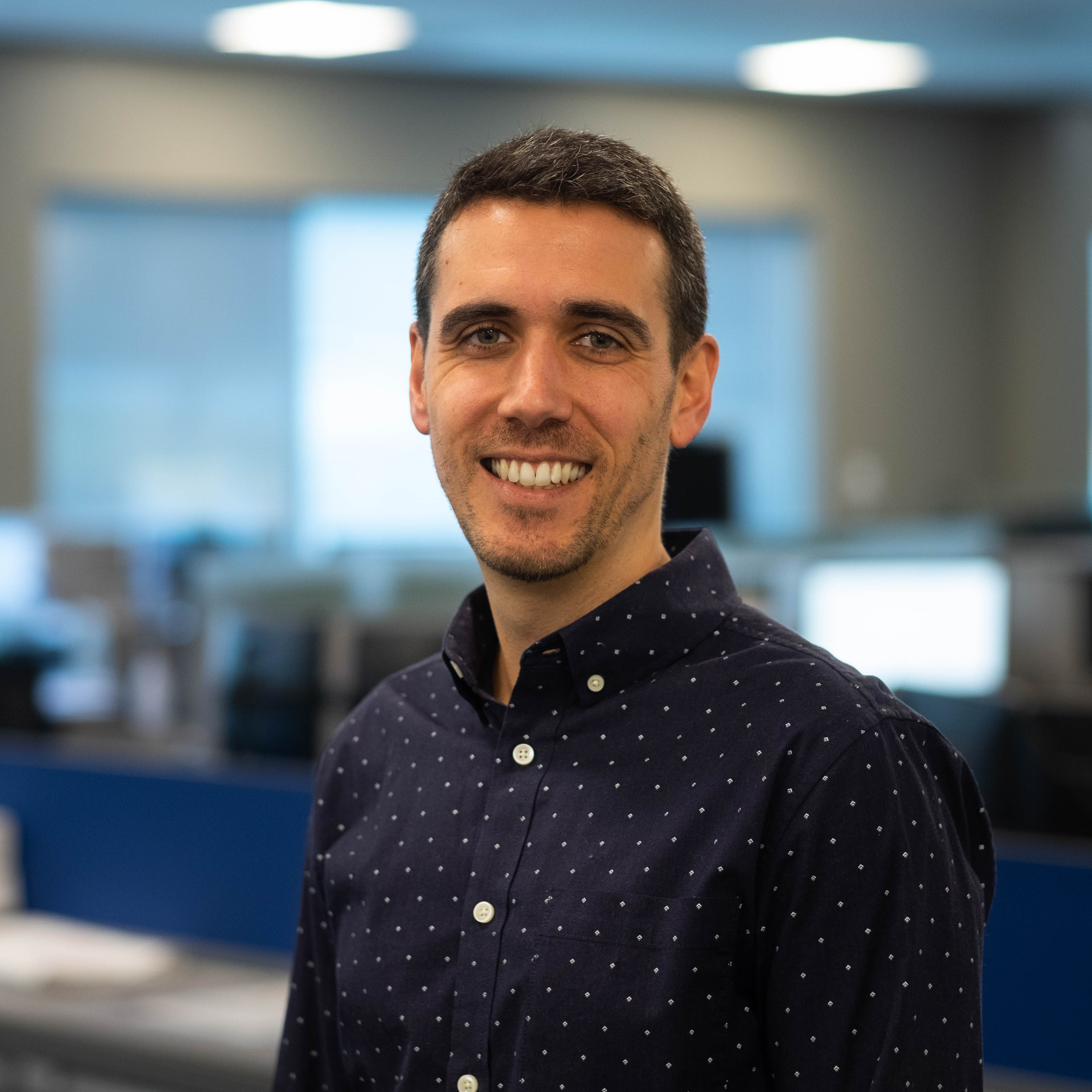