News
Keep Record-Breaking Gas Prices from Slowing Construction On Your Project: Use Modular Construction and Prefabrication To Offset Gas Prices
Soaring prices at gas pumps across the U.S. threaten to further pressure consumers and an economy already struggling with sky-high inflation. And with no foreseeable end in sight, the construction industry stands to take a big hit. What can commercial real estate and construction projects do to offset record-breaking gas prices?
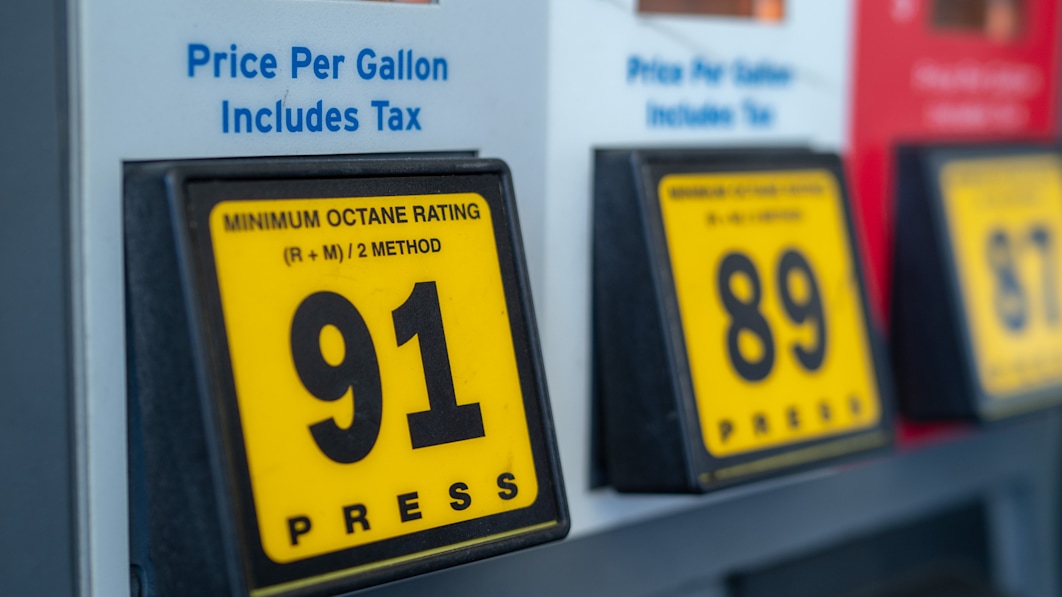
All-Time High Gas Prices
Over the last two weeks, the price for U.S. gasoline hit record highs, the combined effect of a surge in global energy markets and the far-reaching economic consequences of the war in Ukraine. The national average price for regular gasoline hit $4.331 a gallon for regular unleaded and $5.135 for diesel last week, surpassing the previous record of $4.114 reached in July 2008, according to AAA. For comparison, the average price of gas at the same time lastyear was just $2.86 a gallon.
The rise is being driven by strengthening global demand as economies reopen and recover from the pandemic; low inventories as oil producers and refiners struggle to boost output following the pandemic-drive slowdown; and limited supply as traders, shippers, and financiers have shunned supplies of oil from Russia, which is the world’s second-largest exporter of crude oil after Saudi Arabia, according to the International Energy Agency.
Construction Industry Stands To Take A Big Hit
Soaring record-breaking prices at gas pumps across the U.S. threaten to further pressure consumers and an economy already struggling with sky-high inflation. And with no foreseeable end in sight, the construction industry stands to take a big hit. While the industry is not among those heaviest in use of gas, such as horticulture or manufacturing, the construction sector is already struggling with substantially higher building materials prices and supply chain disruptions. High gas prices threaten to diminish industry margins and timelines already plagued by shortages, delays, and cost increases in the building process.
Modular & Prefabricated Construction Methods Can Offset Gas Prices
To offset record-breaking gas prices, the commercial real estate and construction industries must find ways to use less gas. Modular and prefabricated construction methods offer a solution to help AEC industry players cope with the indefinite price spike in fuel.
How Do Modular Construction & Prefabrication Work?
Most of us are probably familiar with conventional construction methods. Used for centuries, “traditional” construction describes linear building methods, where each individual step is not only constructed entirely (or largely) on site, but also needs to be completed before the project can move on to the next phase.
A relatively new trend, modularized construction and prefabrication are the building industry’s answer to existing inefficiencies. Modular construction is an off-site based construction method, during which individual components are manufactured (or ‘prefabricated’) in a factory, transported to the site entirely (or mostly) complete and assembled on location. This method reduces waste – a big problem for the field in 2021 – by producing less and recycling leftover materials. By 2023, the modular construction market is projected to reach a whopping $157 billion.
Fewer Shipments Mean Less Gas
So how do new building methods help offset soaring gas prices? In conventional construction techniques, traditional “stick-built” building elements require many shipments to be made to the jobsite to transport the building materials, crew members, and left-over materials and construction waste away from the job site upon completion. Prefabricated stairs, by comparison, can be transported to the job site in fewer and more compact shipments. Fewer truckloads to and from the job site means less fuel consumption, which can significantly help to offset rising fuel prices.
In our projects, we typically see the number of truckloads required for the transport of building materials diminish by anywhere from 66% to 80%. Just check out Synergi’s work at Walmart’s Home Office, its new headquarters campus. We optimized the design to enable prefabricating 36 stairways, bringing the number of truckloads required to transport the stairs from 108 down to 36 – that’s two-thirds less fuel (and less carbon emissions, to boot!).
Don’t let record-breaking gas prices diminish margins and timelines already plagued by shortages, delays, and cost increases in your building processes. By working modular building and prefabrication into your construction plans, your project can benefit from more efficient transportation. And when that means a reduction in fuel usage – those are some savings we can all get on board with!
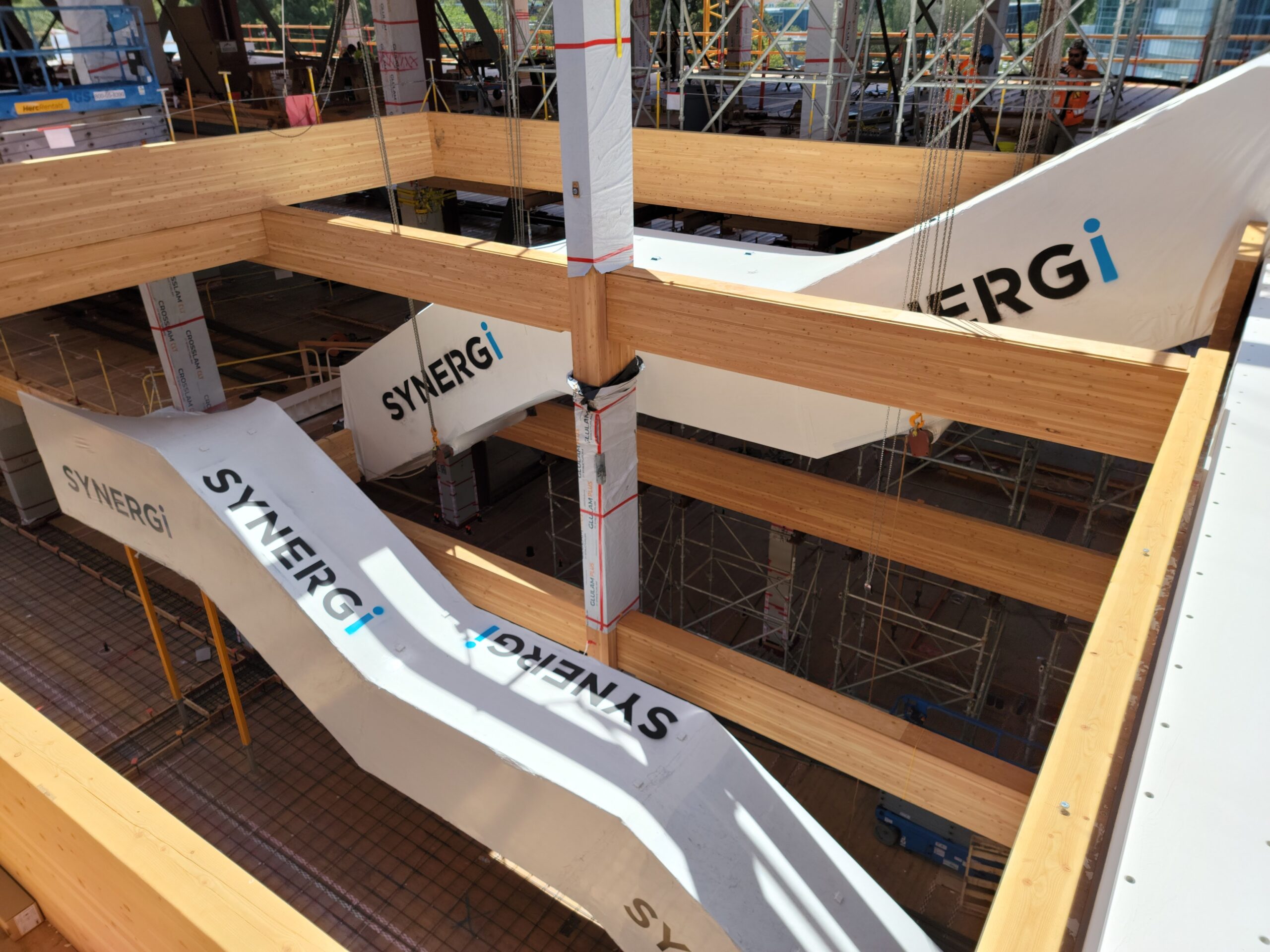
Spotted: Synergi Stairs Featured in Client Video
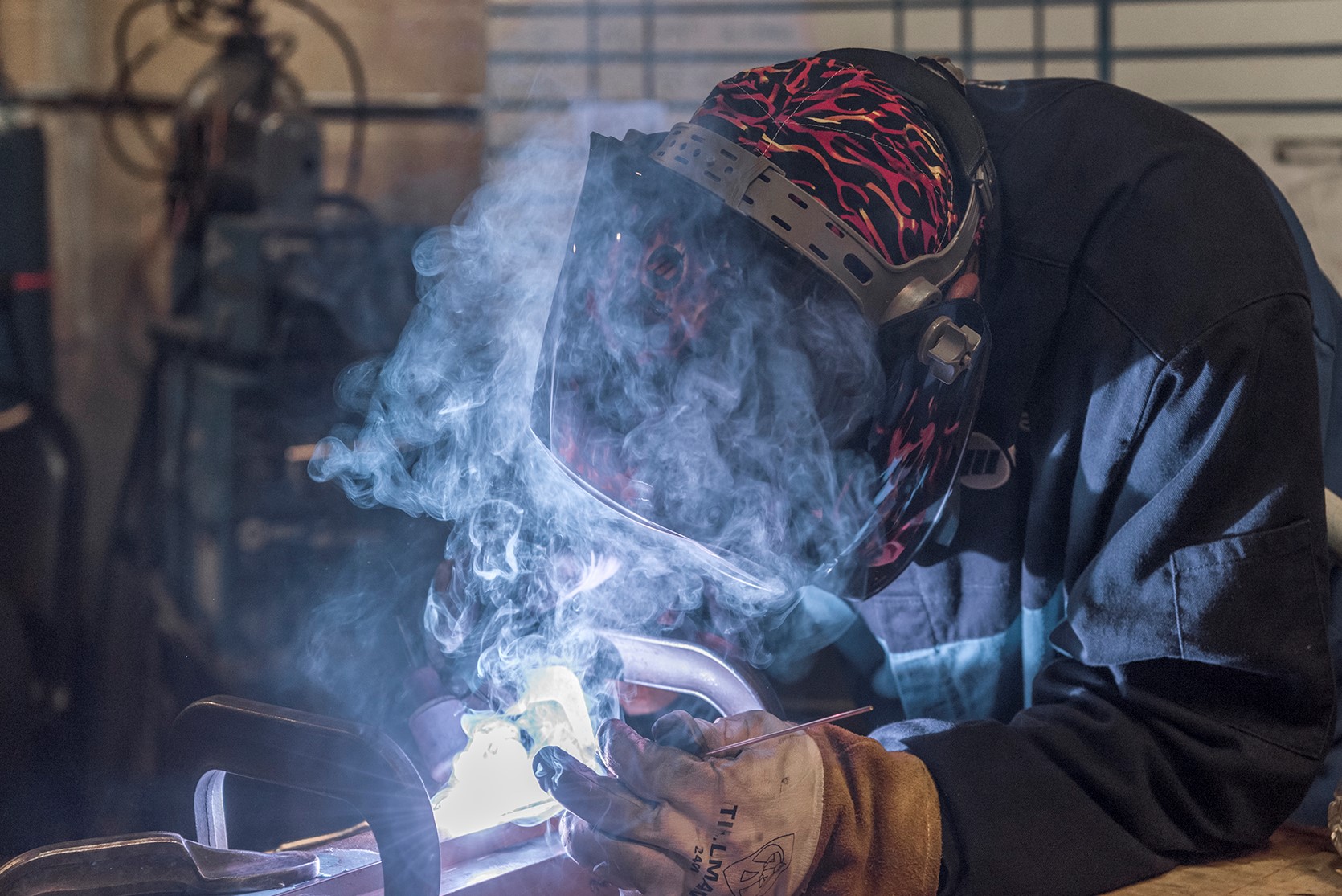